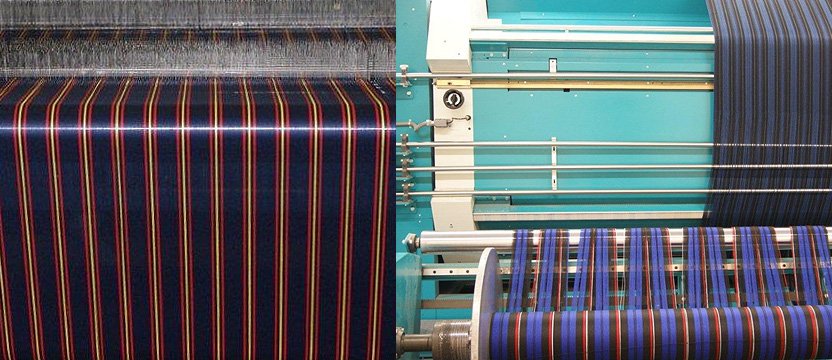
Yarn: A wide range of yarns are stock supported to ensure short lead times are achieved. Several tonnes of top dyed yarn are imported each month and package dyed yarn is delivered from our local spinners where as little as 3kgs can be dyed to match the shade required. Yarn is checked prior to approval for quality and continuity of shade.
Warping: Cone winding prepares the yarn for the warp. Using the latest technology, the Karl Myer warping machine allows flexibility of production. A minimum of 13m can be warped to fulfil small orders or to allow samples to be made prior to commiting to bulk. Up to 16 shades can be used. The VTA warping machine is capable of warping up to 1800m.
Weaving: Investment has been made in the new Sulzer Projectile, G6200 and G6300 weaving machines. 16 machines, combining technology with skilled weavers allows us to produce up to 18,000m of fabric per week. A variety of compositions including poly cotton, poly viscose, poly wool and pure wool, producing plains, checks, tartans and stripes are woven to give us a comprehensive stock supported range of fabrics.
Mending: The fabric is inspected on the perch and any imperfections removed or noted for mending. Skilled burlers and menders check the fabric and rectify any imperfections or faults.
Finishing: We are joint owners of Roberts Dyers and Finishers. In order to impart the required functional properties to the fabric, it is neccessary to subject the material to different types of physical and chemical treatments. For example: crease resist resin, Teflon ® coating, Nanosphere ® technology.
Quality Control: Quality is checked through every part of the production process from the initial submission of yarn through to the finished fabric prior to dispatch. This includes checking continuity of shade, set size, usable width and pilling. Producing high quality fabric is our priority.